前回(第4回)は、DX時代のCAEについて以下のように紹介しました。
デジタルエンジニアリングにおける開発プロセス改革を実現する鍵はCAEであり、従来以上に重要な位置付けになります。製品開発プロセスの各段階に企画CAE、設計CAE、評価CAEという仕組みを構築して組込みます。組込む要点は、プロセス改革の主目的である競争力強化のための最適化と、開発の高効率化や高速化のための手戻り防止を確実に支援することです。
今回(第5回)は、評価CAEの概要と課題について、自動車用エンジン開発を例に検証プロセスと併せて解説します。
検証プロセスの主目的は、製品の企画および設計後に性能目標達成度や市場適合性等を確認することです。エンジンに求められる主要な性能には出力、燃料消費、音振動等があり、企画時に定められた性能目標を達成しなければなりません。企画CAEを活用して各システムを最適設計し目標達成予測を経て、試作した実機で性能目標の達成度を検証することが一般的です。また、エンジンに求められる主要な適合性にはドライバビリティ(応答性や加速性等)、排気ガス(法規や規制)、耐久信頼性等があり、市場での不具合を未然防止しなければなりません。
ここでは、エンジン(ハードウェア)の耐久信頼性を例として市場適合性検証について解説します。
試作および実機検証前に不具合を発見して対策をするために、基本設計後にCAEによる検証を実施します。強度問題等の不具合があれば速やかに設計にフィードバックし、設計変更を行います。これは“小さな”設計手戻りですが、予防したいものです。上流の設計プロセスに設計CAEを組込み、構造最適化と併せて先行検証を実施することで、下流の検証プロセスにおける手戻りを防止することは不可能ではありません。
CAE検証後に試作を行い、実機検証を実施します。耐久試験は、市場での一般的な使われ方よりも厳しい運転条件で実施され、システムの機能や部品の耐久信頼性を検証します。耐久試験に限らず実機検証で不具合が発生すると、設計変更、CAE検証、試作、実機検証という一連のプロセスを繰り返すため“大きな”設計手戻りとなり、試作も含めて多くの費用、工数、時間が必要です。開発の効率やスピードの大幅な向上を目指すのであれば、設計手戻りを未然防止して実機検証は不具合発生無く1回で完了することが理想です。
現時点では、一部の領域でCAEによる解析や評価が難しい技術課題が残されています。主な課題として以下の3項目を紹介します。特に(1)は結果として検証は実機に依存せざるを得ず、設計手戻りにより開発効率やスピードのボトルネックとなる恐れがあります。
(1)CAE評価手法が未確立
・メカニズム解明が十分ではなく、CAEでは解析や評価が難しいこと
(2)官能評価(感性評価)
・物理量と官能量に乖離があり、CAEでは直接の官能評価が難しいこと
(3)さらなる評価精度向上
・最適化を実現するために、実機との相関係数をさらに高めること
(1)CAE評価手法が未確立
不具合等の発生メカニズム解明が十分ではなく、CAEで解析や評価が難しい技術課題です。代表例としては、エンジン潤滑システムにおける軸受の摩耗や焼付き等があります。潤滑システムは、軸と軸受のように相対運動により発生する現象を扱うトライボロジーと呼ばれる工学分野に属します。相対運動だけでなく、表面状態、潤滑状態等の要因が多岐に渡り、原因の解析や特定が難しく、理論に加えて実験も組み合わせて評価する必要があります。
(2)官能評価(感性評価)
物理評価(計測器による評価)と官能評価(感性による評価)の間には多少の乖離があり、CAEによる直接の官能評価にはまだ課題があります。現時点では物理評価による解析や評価を基本とし、最終的には官能評価で良否判定しており、試作した実機による仕様熟成や最終確認が不可欠です。代表例はエンジンのクランクシステム、動弁システム、吸排気システム等から発生するNV(音振動)です。ちなみに、車両における代表的な官能評価は操縦安定性(走る、曲がる、止まる)やNVH(騒音、振動、乗り心地)等があります。
(3)さらなる評価精度向上
最近ではCAE、CAD、最適化ソフトの進化や連成解析の工夫等で、3次元パラスタが現実的な時間内に完了できるようになり、構造(形状)最適化プロセスを設計CAEに組込むことが可能になりつつあります。従来は設計後の検証段階で不具合がなければ開発終了としていましたが、今後は最適化により強度余裕分を積極的に排除して軽量化やコストダウンを狙う設計CAEが普及していきます。ただし、前提条件として強度余裕分をより正確に把握する必要があり、CAEにはさらなる評価精度向上が求められます。なお、最適化は構造系にとどまらず、機構系や流体系にも応用可能です。
評価CAEは構造系に始まり、機構系から流体系、およびそれらの連成へと対象領域を着実に拡大し、設計手戻りの防止に貢献してきました。一方で、CAEによる解析や評価が難しい技術課題が残されています。次回(第6回)は、CAE評価手法が未確立な課題を例に、評価CAEの課題解決手法について解説します。
INDEX
第1回 序 略歴とコラム紹介
第2回 DXとデジタルエンジニアリング
第3回 製品開発プロセスの目指す姿
第4回 DX時代のCAE
第5回 評価CAEの概要と課題
第6回 評価CAEの課題解決手法
第7回 企画CAEの概要と課題
第8回 企画CAEの運用と応用
第9回 設計CAEの概要と課題
第10回 設計CAEの課題解決の進め方
第11回 開発プロセス運用の仕組み作り
第12回 まとめと変革の時代に求められるエンジニア像
著者ご紹介
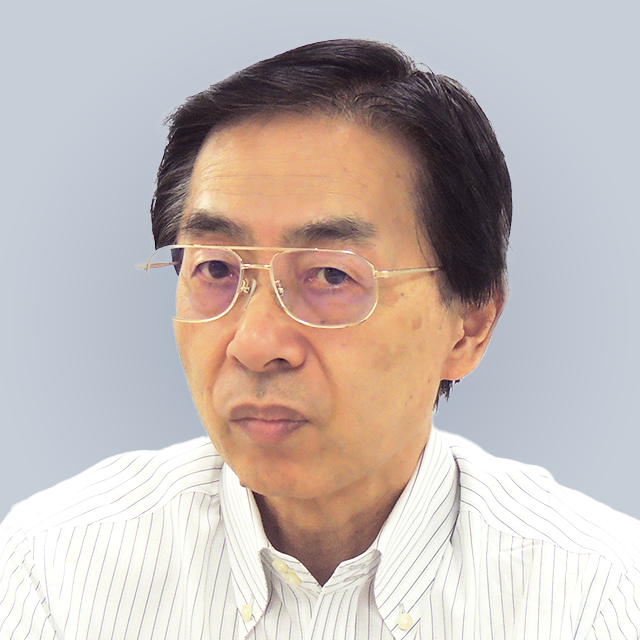
品川エンジニアリング株式会社
(技術コンサルティング)
プロメテック・ソフトウェア株式会社顧問
品川 博 様
プロフィールを見る
1979年
㈱本田技術研究所 入社(四輪R&Dセンター)
- エンジン設計(基幹部品)
- エンジン設計部門長
- パワートレイン開発部門長(米国研究所)
- 開発プロセス改革(MBD/MBSE、設計基準構築等)
2016年
品川エンジニアリング㈱ 設立(技術コンサルティング)
- MBD/MBSE、開発プロセス改革等
- プロメテック・ソフトウェア顧問